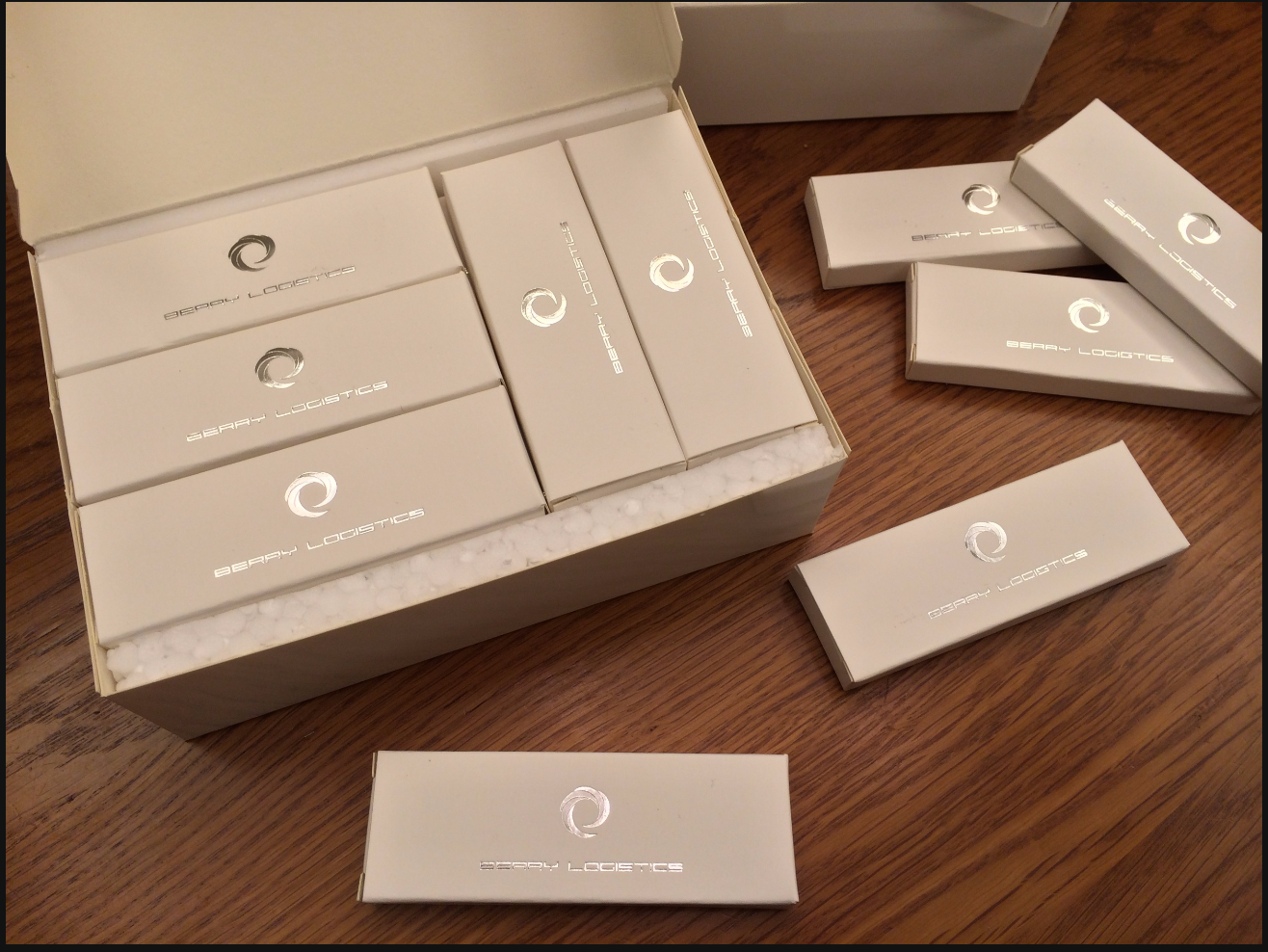
Berry Logistics
My Role
Co-founder
Project Type
Business Development & Product Design
Team
Darren Hou, Sean Hsu
The Problem: mishandling
RE-INSPECTION
The average warehouse distribution center spends 48.8 hours man-hours per day inspecting and procesing mishandled packages
Damages
In 2013, for U.S Home Appliances alone, over $1.3 billion dollars in damages were directly caused by mishandling
concern
Customer discovery has shown that over 77% of E-commerce consumers express worry or concern about the shipping and handling process
THE SOLUTION: The berry tag
In response, we created the Berry Tag, a low-cost impact sensor that simply and visually communicates a package's shipping and handling information.
Berry Tags are applied on the outside of a product's packaging so logistics personnel can easily identify whether or not a package has been mishandled. Whenever a package is mishandled, the tag will change from white to red.
EFFICENCY
Berry Tags help logistics providers be more efficient. The Berry Tag provides logistics providers with more information, identifying opportunities for optimization.
consumer confidence
Berry Tags increase business and consumer confidence. Berry Tags streamline the damage claims by a clear means of accountability.
REVENUE
Berry Tags help business partners make more money. By integrating the Berry Tag as part of their services, partners would be able to generate profit off each unit sold.
The process
phase 1
- Market research and discovery
- Interviewed and surveyed over 100 potential users
- Product prototyping via 3D Printing
Phase 2
- Pitched at multiple entrepreneurship competitions
- Extensive product development
- Contracted a Taiwanese injection molder for initial production
PHASE 3
- Live trial with Taiwanese E-commerce platform
- Third cycle of product development integrating trial feedback
After 16 months and tens of thousands of dollars, we were ultimately unsuccessful.
As of April 15, 2014 - Berry Logistics no longer exists as a business entity. Here's what I learned in the process:
LESSONS LEARNED
- Have one clear business model. As a first-time founder, having multiple business models may sound like a plus. Flexibility sounds like an upside, but to serious investors - this flexibility is simply perceived as a lack of research.
- Respect legacy market behavior. One of the key reasons we were didn't succeed is because we did not adequately account for how existing practices and partnerships in the logistics industry would work with the Berry Tag. We were too focused on solving the problem of mishandling and failed to address how implementing the Berry Tag might affect other existing practices.
- Be deeply passionate about what you're building if you're going to pursue entrepreneurship. In the case of Berry Logistics, I co-founded a company because I saw a strong business opportunity and simply had a desire to build something, not because I was singularly obsessed with supply chain transparency.
That being said, our efforts did not go without recognition. Here are some awards we won along the way: